Comprehending the Key Elements and Fixing Methods for Packaging Machine Upkeep
Effective maintenance of packaging makers pivots on an extensive understanding of their essential elements, consisting of the frame, drive system, and sealing systems. Identifying common maintenance issues, combined with the application of preventative approaches and troubleshooting methods, can dramatically boost machine reliability.
Key Parts of Packaging Machines
Product packaging devices contain a number of crucial parts that function with each other to make certain effective and efficient packaging procedures. At the core of these equipments is the structure, which gives architectural honesty and houses the numerous operating components. The drive system, usually a mix of electric motors and equipments, assists in the motion of components, enabling precise operation throughout the packaging cycle.
An additional crucial part is the conveyor system, which delivers products through different phases of the product packaging process. This is frequently complemented by sensing units and controls that check the setting and speed of things, making certain synchronization and decreasing errors. The filling up system is crucial for properly giving the right amount of product into plans, whether in fluid, powder, or solid kind.
Sealing devices, including heat sealants or sticky applicators, play a vital function in securing plans, protecting against contamination and prolonging service life. Furthermore, labeling systems are important for giving necessary item information, making sure compliance with laws. The control panel, geared up with user-friendly interfaces, enables drivers to manage maker functions, screen efficiency, and make adjustments as needed, making sure optimum efficiency and performance in packaging operations.
Typical Upkeep Concerns
Effective procedure of product packaging machines depends heavily on normal upkeep to avoid typical issues that can interrupt manufacturing. Amongst these concerns, mechanical damage prevails, especially in elements like motors, seals, and conveyors, which can cause unanticipated downtimes. In addition, imbalance of components can cause ineffective procedure, creating items to be improperly packaged or harmed during the process.
One more typical maintenance problem involves the build-up of dust and debris, which can interfere with the device's sensors and relocating components. packaging machine repair service. This not only impacts performance but can also position security dangers. Lubrication failings can lead to boosted rubbing, resulting in overheating and eventual part failing.
Electrical issues, usually originating from loosened connections or damaged circuitry, can interrupt machinery functions, leading to substantial production delays. Last but not least, software glitches as a result of incorrect configurations or out-of-date programs can impede the machine's operation, necessitating prompt treatment. Addressing these typical upkeep problems proactively is important for making certain ideal performance and durability of packaging machinery.
Preventative Upkeep Techniques
Applying preventative maintenance strategies is vital for sustaining the effectiveness and integrity of packaging devices. These methods include an organized method to upkeep, focusing on the regular evaluation and servicing of devices to preempt possible failures. By adhering to an arranged maintenance program, drivers can identify deterioration on parts prior to they lead to substantial break downs.
Crucial element of a preventative maintenance technique include routine examinations, lubrication, cleaning, and element replacements based on supplier referrals. Utilizing checklists can streamline this process, guaranteeing that no crucial jobs are ignored. Furthermore, keeping exact documents of maintenance tasks help in tracking the device's performance gradually, promoting educated decision-making pertaining to future upkeep demands.
Training staff on the value of preventative upkeep improves compliance and promotes a society of aggressive treatment. Applying an anticipating maintenance component, utilizing information analytics and sensor modern technology, can further optimize machinery performance by predicting failings before they take place.
Repairing Methods
When faced with malfunctions or inefficiencies in product packaging devices, utilizing methodical troubleshooting techniques is necessary for determining and dealing with issues swiftly. The initial step in reliable troubleshooting is to establish a clear understanding of the device's operational parameters and efficiency metrics. This includes reviewing the machine's requirements, in addition to any kind of error informs or codes presented.
Next, image source drivers should carry out a visual examination, inspecting for noticeable indicators of wear, damages, or imbalance. This usually consists of analyzing belts, equipments, and sensing units to identify prospective reasons of breakdown. Gathering functional information, such as production prices and downtime logs, can also provide insights into reoccuring problems.
When possible troubles are identified, utilizing a sensible Get More Info technique to isolate the origin cause is essential. This might require screening individual elements or systems in a regulated manner. Taking part in conversations with operators who engage with the machinery consistently can produce useful feedback regarding unusual behaviors or patterns.
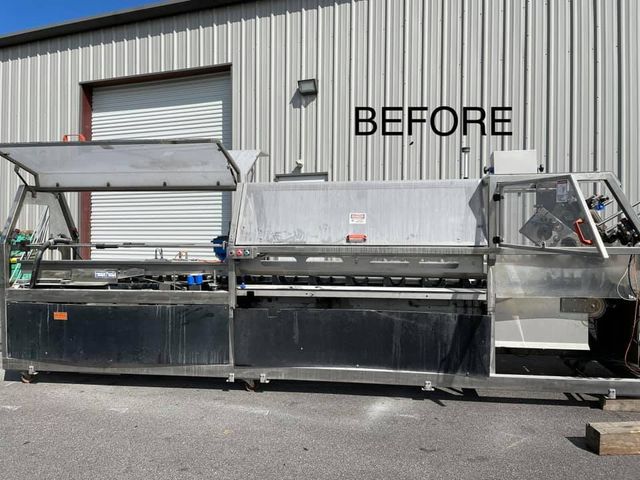
Repair and Replacement Ideal Practices
A thorough understanding of repair work and substitute finest techniques is essential for maintaining the durability and efficiency of packaging makers. Regularly examining the condition of maker parts enables timely treatment, stopping more significant problems that can lead to costly downtimes.
When top article fixings are essential, it is vital to make use of OEM (Original Tools Supplier) components to ensure compatibility and performance. This not just maintains the honesty of the maker but likewise upholds guarantee arrangements. Additionally, it is a good idea to preserve a stock of vital extra parts to help with fast substitutes and decrease operational interruptions.
For intricate repairs, engaging licensed professionals with specialized training in packaging equipment is advised. They have the experience to diagnose concerns precisely and execute fixings efficiently. Additionally, documenting all repair service tasks and parts replacements is critical for maintaining a comprehensive maintenance history, which can aid in future troubleshooting.
Last but not least, implementing a proactive approach, consisting of normal inspections and predictive maintenance techniques, boosts the integrity of product packaging makers. By sticking to these finest methods, services can guarantee optimal machine efficiency, minimize operational dangers, and extend tools life-span.
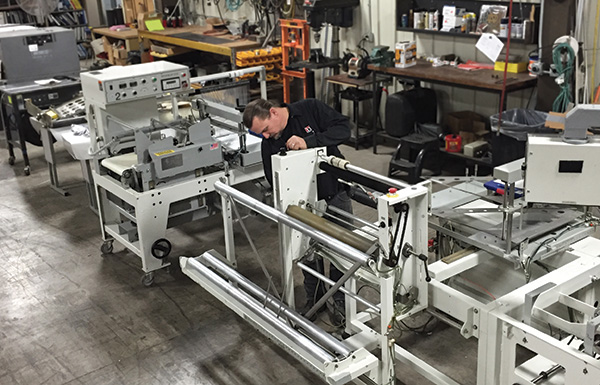
Verdict
In conclusion, an extensive understanding of product packaging equipment parts and effective maintenance strategies is important for ideal efficiency. By carrying out these techniques, companies can make certain the long life and performance of product packaging equipments, ultimately contributing to improved functional performance and lowered prices (packaging machine repair service).
Reliable upkeep of product packaging equipments pivots on a detailed understanding of their vital parts, including the framework, drive system, and sealing mechanisms.Effective procedure of product packaging makers depends greatly on regular maintenance to stop typical problems that can disrupt production.Applying preventative upkeep methods is important for sustaining the efficiency and reliability of product packaging makers. Additionally, maintaining exact records of maintenance tasks help in tracking the device's performance over time, promoting notified decision-making regarding future upkeep requirements.